Exploring the Numerous Techniques and Technologies Behind Plastic Extrusion
The world of plastic extrusion is a mix of modern technology, accuracy, and innovation, critical to various sectors worldwide. Advanced machinery, digital controls, and a range of products assemble in this complicated procedure, generating high-quality, long lasting items.
Recognizing the Basics of Plastic Extrusion
The procedure of plastic extrusion, often hailed as a keystone in the realm of manufacturing, creates the bedrock of this discussion. In significance, plastic extrusion is a high-volume manufacturing process in which raw plastic product is thawed and formed right into a constant profile. The process begins with feeding plastic products, typically in the type of pellets, right into a heated barrel.
The Role of Various Products in Plastic Extrusion
While plastic extrusion is a generally used method in production, the materials utilized in this procedure substantially affect its final result. Various kinds of plastics, such as pvc, polyethylene, and abdominal, each provide special buildings to the end product. Manufacturers have to meticulously think about the residential or commercial properties of the material to optimize the extrusion process.
Techniques Utilized in the Plastic Extrusion Refine
The plastic extrusion procedure involves various methods that are essential to its operation and effectiveness (plastic extrusion). The conversation will start with a simplified description of the basics of plastic extrusion. This will certainly be complied with by a break down of the process thoroughly and an exploration of techniques to boost the effectiveness of the extrusion strategy
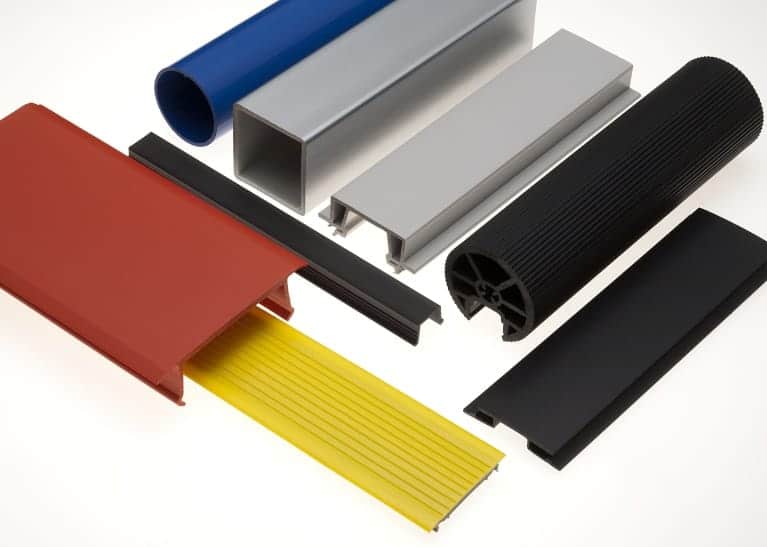
Understanding Plastic Extrusion Essentials
In the realm of manufacturing, plastic extrusion stands as an essential process, crucial in the production of a plethora of daily products. At its core, plastic extrusion involves transforming raw plastic product into a constant profiled shape. This is attained by thawing the plastic, commonly in the form of granules or pellets, and compeling it through a designed die. The resulting product is a long plastic item, such as a pipeline, panel, or wire finish, that maintains the shape of the die. This economical method is extremely functional, able to create complicated shapes and suit a variety of plastic materials. Basic understanding of these basics allows for additional exploration of the much more intricate elements of plastic extrusion.
Comprehensive Extrusion Process Break Down
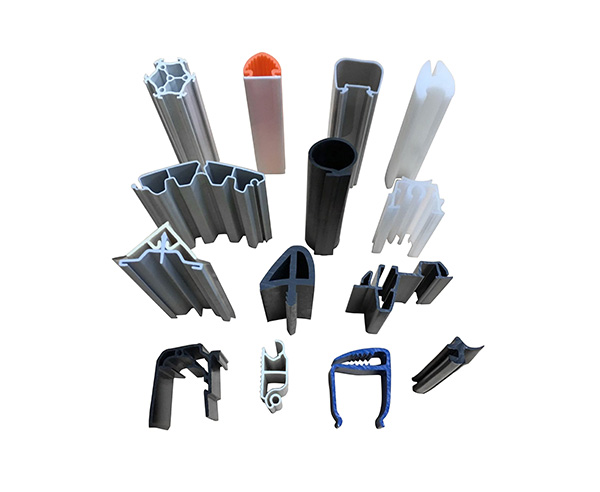
Improving Extrusion Strategy Efficiency
Effectiveness gains in the plastic extrusion process can considerably impact both the quality of the last product and the total productivity of the procedure. Continual optimization of the extrusion strategy is vital to preserving an one-upmanship. Strategies find more that improve efficiency typically involve precise control of temperature and pressure throughout the procedure. Modern modern technologies, such as digital systems and sensors, have actually been critical in attaining this control. The usage of high-grade raw materials can lower waste and improve outcome high quality. Regular upkeep of extrusion equipment can also minimize downtimes, thus increasing performance. Lastly, taking on lean production concepts can assist eliminate unneeded action in the process, promoting effectiveness gains.
How Innovation Is Changing the Face of Plastic Extrusion
The introduction of new technology has actually considerably changed the landscape of plastic extrusion. It has actually caused the advancement of advanced extrusion machinery, which has actually enhanced the performance and quality of the plastic extrusion process. Additionally, developments in the extrusion process have likewise been driven by technological advancements, offering enhanced capabilities and adaptability.
Advanced Extrusion Equipment
Revolutionizing the world of plastic extrusion, advanced equipment imbued with sophisticated innovation is ushering in a new age of performance news and precision. These equipments, furnished with cutting-edge attributes like automatic temperature control systems, make certain optimum problems for plastic handling, thereby lessening waste and improving product high quality. High-speed extruders, for example, enhance result rates, while twin-screw extruders offer premium blending capabilities, vital for creating complicated plastic blends. Furthermore, digital control systems use unmatched accuracy in operations, lowering human mistake. These machines are designed for durability, reducing downtime and upkeep costs. While these improvements are already remarkable, the continual development of technology promises even better jumps forward in the field of plastic extrusion machinery.
Technologies in Extrusion Processes
Taking advantage of the power of contemporary innovation, my review here plastic extrusion processes are undertaking a transformative transformation. With the advent of 3D printing, the plastic extrusion landscape is likewise increasing into brand-new realms of possibility. These technical developments are not just improving the high quality of extruded plastic items yet additionally driving the sector towards a much more lasting, reliable, and cutting-edge future.
Real-World Applications of Plastic Extrusion
Plastic extrusion, a efficient and versatile process, locates usage in countless real-world applications. The auto industry additionally harnesses this modern technology to generate components like trim and plastic bed linen. The stamina and flexibility of plastic extrusion, paired with its cost-effectiveness, make it a vital procedure throughout different industries, underlining its prevalent sensible applications.
The Future of Plastic Extrusion: Trends and forecasts
As we look to the perspective, it becomes clear that plastic extrusion is positioned for substantial developments and transformation. Environment-friendly choices to typical plastic, such as bioplastics, are additionally expected to gain traction. These fads indicate a vibrant, evolving future for plastic extrusion, driven by technological innovation and a commitment to sustainability.
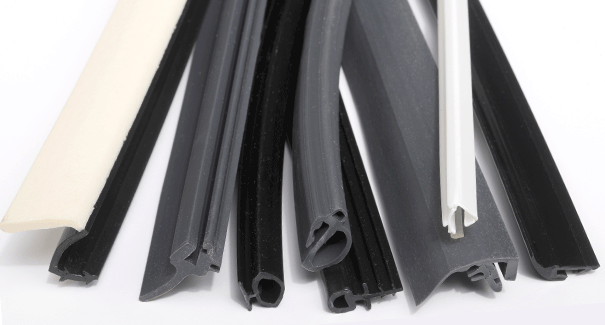
Final thought
In final thought, plastic extrusion is an intricate process that makes use of sophisticated innovation and differed materials to create varied items. As plastic production continues to advance, it stays a necessary component of numerous industries worldwide.
In essence, plastic extrusion is a high-volume manufacturing procedure in which raw plastic material is melted and formed into a constant account.While plastic extrusion is a typically used method in production, the products utilized in this procedure substantially influence its final result. At its core, plastic extrusion entails transforming raw plastic product right into a continuous profiled form. It has actually led to the growth of sophisticated extrusion equipment, which has improved the performance and high quality of the plastic extrusion process.In conclusion, plastic extrusion is a complex process that utilizes sophisticated innovation and differed products to produce varied items.